For years, lab teams have relied on Excel spreadsheets to manage equipment, schedule usage, and track maintenance. While spreadsheets may have been sufficient for smaller setups, today’s R&D labs, especially in pharma, biotech, and academic research, have outgrown them.
If your lab is still operating with Excel or other manual methods, here’s why it’s time to reconsider, and what modern lab operations leaders are doing instead.
The problem with managing lab equipment in Excel
Spreadsheets are everywhere. But in modern R&D environments where hundreds or even thousands of instruments are used across global teams, Excel becomes a bottleneck. Here’s why:
- No real-time visibility: You can’t know which equipment is available, booked, or out for maintenance without manual updates.
- High risk of human error: A simple typo can lead to double bookings, missed calibrations, or worse, compromised experiments.
- No automation: Maintenance reminders, usage tracking, and approvals must all be done manually.
- Scattered information: Data lives in silos across files, emails, LIMS, ERP systems, and paper logs.
- Lack of scalability: As labs grow in size and complexity, Excel simply can’t keep up.
In short, Excel was never designed to manage the complexity of modern lab infrastructure.
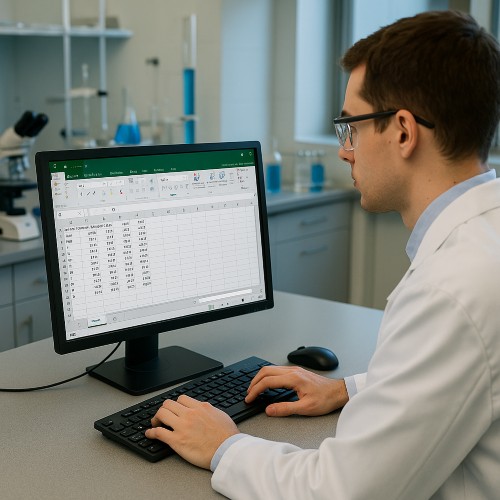
The cost of manual lab management
Relying on Excel or legacy systems often leads to:
- Inefficient equipment utilization → Underused or overbooked instruments.
- Duplicate purchases → No central visibility results in redundant procurement.
- Downtime and delays → Missed service events disrupt critical research timelines.
- Wasted time → Scientists and lab managers spend hours chasing data instead of focusing on science.
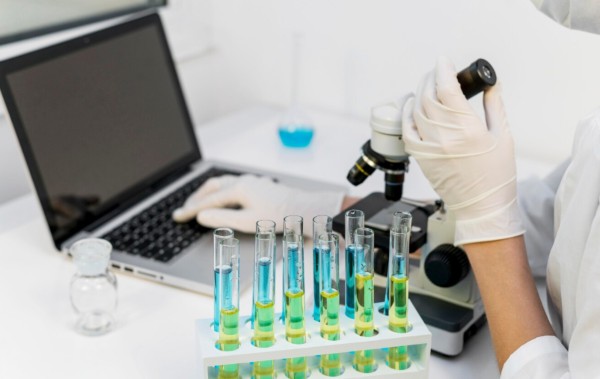
How newLab® solves the problem
New-generation lab management platforms like newLab® offer a smarter way to manage lab operations, digitally, intelligently, and at scale. Built natively on ServiceNow, newLab® eliminates the limitations of spreadsheets with:
- Centralized Equipment & Resource Management
Track every lab asset in real-time. Know what’s in use, what needs maintenance, and what can be shared across teams—across all lab sites.
- Smart Scheduling & Usage Optimization
Automated booking and scheduling tools reduce conflicts, improve utilization, and ensure availability when and where it’s needed.
- Preventative Maintenance Insights
Avoid unexpected breakdowns with 360° visibility into equipment status, service history, and performance metrics.
- Enterprise Integration (No Data Silos)
newLab® integrates seamlessly with existing systems like LIMS, ELN, ERP, and ServiceNow—unifying data and eliminating duplicate work.
- Automated Workflows
From service requests to equipment onboarding, digital workflows save time and reduce manual effort.
Request a demo of newLab® today and discover how much time, money, and stress you can save.
The ROI of ditching Excel
Labs that switch from Excel to a connected digital platform often see:
- 30–40% reduction in equipment downtime
- 20% fewer unnecessary equipment purchases
- 50% reduction in manual entry and reporting tasks
- Faster time-to-experiment and fewer delays
You save time, reduce costs, and make better use of your lab investments.
Ready to leave Excel behind?
If you’re still managing your lab with spreadsheets, it’s time to consider a platform purpose-built for R&D.
It’s time to modernize how your lab works. Discover how newLab® can streamline your equipment management and unlock efficiency at every step.